Muller 2200
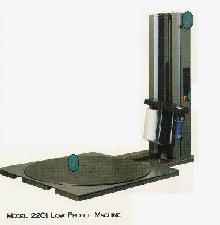
Overview
The Muller 2201 Low Profile, and the 2203 High Profile, Semi-automatic Turntable
Stretch Wrapper uses low cost 20" width film to process 25 to 35 loads
per hour. An optional 30" film delivery system is available to improve
speed, but at a higher minimum film cost per pallet load. A unique modular
design allows greater interchangeability of elements, giving you total control
in designing a wrapper to your individual specifications.
Turntable Advantages
- The small footprint of the 2201 saves valuable floor space.
- Being forklift portable, and using a standard 120 VAC recepticle for power,
allows the machine to be readily moved to maximize the efficiency of your
changing product flows.
- The 2201 turntable machines tend to be more cost effective semi-automatic
wrapping solutions.
Standard Machine Specifications
Download: GAP
2201 - Machine Specifications.pdf
Download: GAP
2203 - Machine Specifications.pdf
Performance
- Production speeds of up to 40 loads per hour
- Standard Load Size: 48"L x 48"W
- Standard Load Diagonal: 68"
- Standard Load Height: 90"H (with 20" film width)
- Maximum Load Capacity: 4,000 lbs. (up to 6,000 lbs.)
Film Delivery
- ST2000 20" carriage (30" carriage available)
- Virtually no neckdown
- Power assisted prestretch (Strain Gauge feedback)
- Prestretch ratio from 100% to 300%
- Standard prestretch ratio is 200%
- Lubrication free on prestretch gear system
- Tilted low profile film carriage allows wrapping below the turntable
surface
- Fully adjustable electronic film force control
Electrical Data
- 120 VAC, single phase, 15 AMP, 60 Hz
Turntable
- 58" diameter, �" steel plate
- 8 cam bearing supports
- Turntable height: 3-1/4" from floor
- Turntable safety skirt
Turntable Drive
- � HP 90 VDC motor
- Variable speed DC control complete with adjustable accel/decel
- Spring tensioned #50 chain drive with guide
- Rotation speed up to 12 RPM
- Positive position turntable alignment
Carriage Lift System
- Dual #40 chain lifting system
- � HP 90 VDC motor
- Variable speed DC control complete with dynamic braking
- ACLA roller guides
- Separate up/down speed adjustment
Frame Construction
- Forklift portable from either end
- Formed steel tower, (bolt on tower extensions available)
- Clean design for maximum safety
- �" thick steel circular skirting around turntable (optional)
- 6061 machine aluminum carriage frame for durable yet lightweight operation
- Light bronze and dark bronze paint scheme
- 1,400 lbs. approximate shipping weight
- Ships fully assembled
Operating Controls
- Omron PLC
- Wrap Up cycle
- Wrap Up/Down cycle
- Low load banding cycle
- Reinforce wrap cycle
- Cycle pause feature
- Life cycle counter (PLC based)
- High speed wrap counting system
- Film force adjustment
- Film carriage Up/Down jog
- Turntable jog button
- Top wrap selector (0 - 9)
- Bottom wrap selector (0 - 9)
- Programmable overwrap adjustment (with auto-height option)
- NEMA 12 dust tight enclosure
- Industrial grade NEMA 4 pushbuttons
- Adjustable top and bottom carriage limits
- Illuminated cycle start/stop button
Documentation
- Mechanical and electrical schematics
- Technical operating and maintenance manual
Safety
- Power disconnect switch
- MCR electric safety circuit
- Push/Pull mushroom emergency stop button
- Quick release safety fuse holders
Common / Standard Options
- Extended Wrap Height Capacity (tower extension)
- Extended Load Diagonal (extended base)
- Heavier Load Capacity
- High Profile Design
- Heavy Duty Ramp
- 220/240 VAC, Single Phase, 50/60 Hz Power
- 30" Powered Prestretch Film Carriage
- Pak-Air Film Carriage
- Turntable Safety Skirt
- 72" Turntable Diameter
- High Speed Turntable
- Manual or Automatic Top Platen
- Dual Turntable
- Turntable Roller Conveyor
- Cold Temperature Operations
- Weigh Scale Systems
Please Note: The above list does not represent all
options available
for this machine. Please contact us for
more information.
|
|