Muller SG3000 Film Carriage
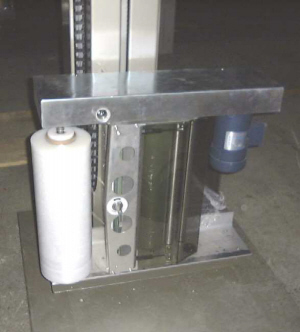 An
evolutionary advancement in the state-of-the-art stretch
wrapping technology, the technology long used for all Octopus
stretch wrapper ST2000 Film Carriages has been ported over
for use on all models and styles of stretch wrapping machines.
The new SG3000 Film Carriage retains the benefit of strain
gauge technology (long present in all Muller higher end
semi-auto and automatic stretch wrapping systems) while
adding the ease of loading and safety features previously
only available on the Octopus' ST2000 Film Carriage . The
SG3000 Film Carriage is also available as an easy to install
retrofit to your existing equipment, there is no reason
your stretch wrapping systems can't take andvantage of the
best the industry has to offer!
This film carriage is now the standard on
most conventional pallet stretch wrapping machines throughout
the Muller line. This carriage has demonstrable superiority
over older and competitor designs. The primary advantages
of the design are reliability, ease of film loading, long
term consistency of prestretch levels, and stretchwrap film
savings.
|
|
Ease
of Film Loading
Changing the film roll is easier and faster
due to the front mounted film threading gate, which allows
the operator to safely pull film through the 20" carriage
without having to thread the film manually. Film threading
through the prestretch rollers is easier and faster due
to the plexiglass gate with safety switch which allows
the operator to pull film through and close the gate for
automatic threading. This is a vast improvement over previous
designs which required the operators to thread the film
through the actual prestretch rollers while manually rotating
the rollers by hand.
Reliability of Operation
The patented Strain Gauge Film Force control
with analog feedback is an electronic
film feed tension-sensing system designed to greatly optimize
film tension, thus reducing the chance of broken film. Reliability
is further enhanced through the tried and true engineering
principle of eliminating moving parts. Older and competitor
designs use a spring-mounted pivoting dancer roller arm
(often called a 'dancer bar') to sense and accommodate the
variable film feed rates required by irregularly shaped
loads. The SG3000's patented electronic film feed tension
sensing system eliminates the need for a moving dancer bar
assembly. This design has proven itself to very reliable,
reducing maintenance costs, and valuable downtime. At the
same time, this zero inertia fixed-mount roller provides
a faster response to load irregularities, automatically
adjusting the film delivery speed to keep a constant film
force-to-load regardless of load position, size, or shape.
|
Stretchwrap
Film Savings
With the analog feedback greatly optimizing
film tension, it is possible for you to either increase
the prestretch level, or convert to a lower gauge film.
In many instances, customers have had no problem accomplishing
both! So with a higher prestretch and/or a lower gauge film,
and increased reliability reducin g
unwanted downtime and maintenance costs, you can wrap more
loads, with a more consistent film tension, all while using
less film. It's money in the bank!
Long Term Consistency of Prestretch Levels
The primary problem with any prestretch
carriage is that as the springs in the tension rollers
grow weak and the pre-stretch rollers wear down with long
term use, the film will have a tendency to pull through
the prestretch carriage without stretching the film. It
will simply slip through. To combat this, the Muller SG3000
has the film path arranged in such a way that the film
wraps around the circumference of the prestretch rollers
to the maximum extent possible. The end result is a consistently
higher prestretch level over the long term.
Safety
The totally enclosed pre-stretching mechanism
can only be accessed (for changing of the film or maintenance)
through an electrically interlocked door. There is no
way for operators or maintenance personnel to access the
rollers without the power to this device being disabled,
even if they forgot to de-energize the machine as per
standard operating procedures and posted notices. This
design commonly satisfies all Pre-Start Safety Review
(PSR) concerns.
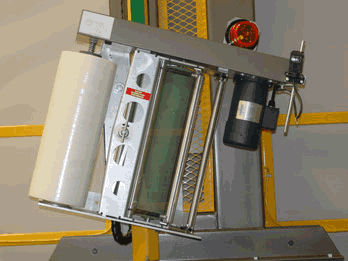
|
|
Standard Specifications
- 1/2 HP 90V DC Variable Speed motor/reducer, high quality Dart
DC/SCR controller.
- Electronic strain gauge tension roller replaces the spring-mounted
pivoting dancer roller arm.
- Zero inertia fixed-mount roller reduces maintenance while
the faster response design adjusts the film delivery speed to
keep a constant film force-to-load regardless of load position,
size or shape.
- Spring-loaded pressure roller offers a maintenance-free, continuously
self-adjusting design to prevent film slippage, inconsistent
stretch levels, and excessive film wrapping costs.
- Lubrication-free direct gearing prestretch ratio control eliminates
conventional chains, sprockets and take-up idlers for virtually
maintenance-free operation.
- The lowest film web neckdown of any powered film prestretch
carriage in the industry.
- The SG3000-20" will handle films from 0.4 mil to 1.35 mil
and prestretch ratios up to 400%.
|
SG3000 Film Carriage Retrofit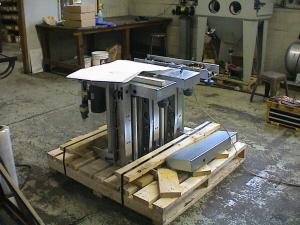
Specifically designed to easily retrofit
onto any conventional stretch wrapper design, semi-auto
or automatic, turntable or rotary arm style machine, the
advantages of the SG3000 can be realized in your application.
GAP skilled and knowledgable Installation Technicians can
retrofit this product onto your equipment.
|
The scope of work required to accomplish the installation of
the SG3000 retrofit requires (but is not limited to) the following:
- Mechanically, and electrically remove the existing Film Carriage,
replacing it with the quoted model SG3000
- Includes necessary engineering and production of a customized
Retrofit Technical Manual.
- Includes necessary PLC program changes and optimizations to
the wrap cycle.
- Includes system power up check; run and production testing.
- Also included is the time for one GAP technician to be present
for the production startup, to address any issues that may arise
when running actual product, and to provide training to your
operators and maintenance staff.
- INSTALLATION NOTE: - This project is likely to require some
cutting, welding, grinding, etc. Use of your fabrication facilities
and/or the assistance of your plant personnel should be expected.
|
|
|
Black
Wire Mesh Safety Cover Upgrade
When the economics of a retrofit film carriage don't make sense, the
issue of changing the film safely can still be dealt with through the
installation of a Black Wire Mesh Safety Cover which shares the advantage
of forcing the door to be opened to thread the film, and at the same time
electrically disengaging the film carriage power, even in the event that
the operator forgets to turn off the power.
Features:
-
available for about 1/5 the cost of a new retrofit film carriage
-
safer to change film
-
retrofittable to any previous model Muller film carriage
-
can be installed, on site, in about a half day
-
most older film carriages can be geared up to 225% prestretch
during the retrofit of the Safety Cover
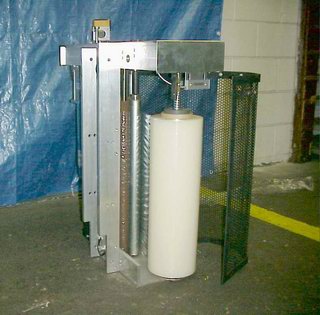
Contact Us for details.
|
|